ジャストインタイム方式とは?メリットやデメリット、企業の導入事例を紹介
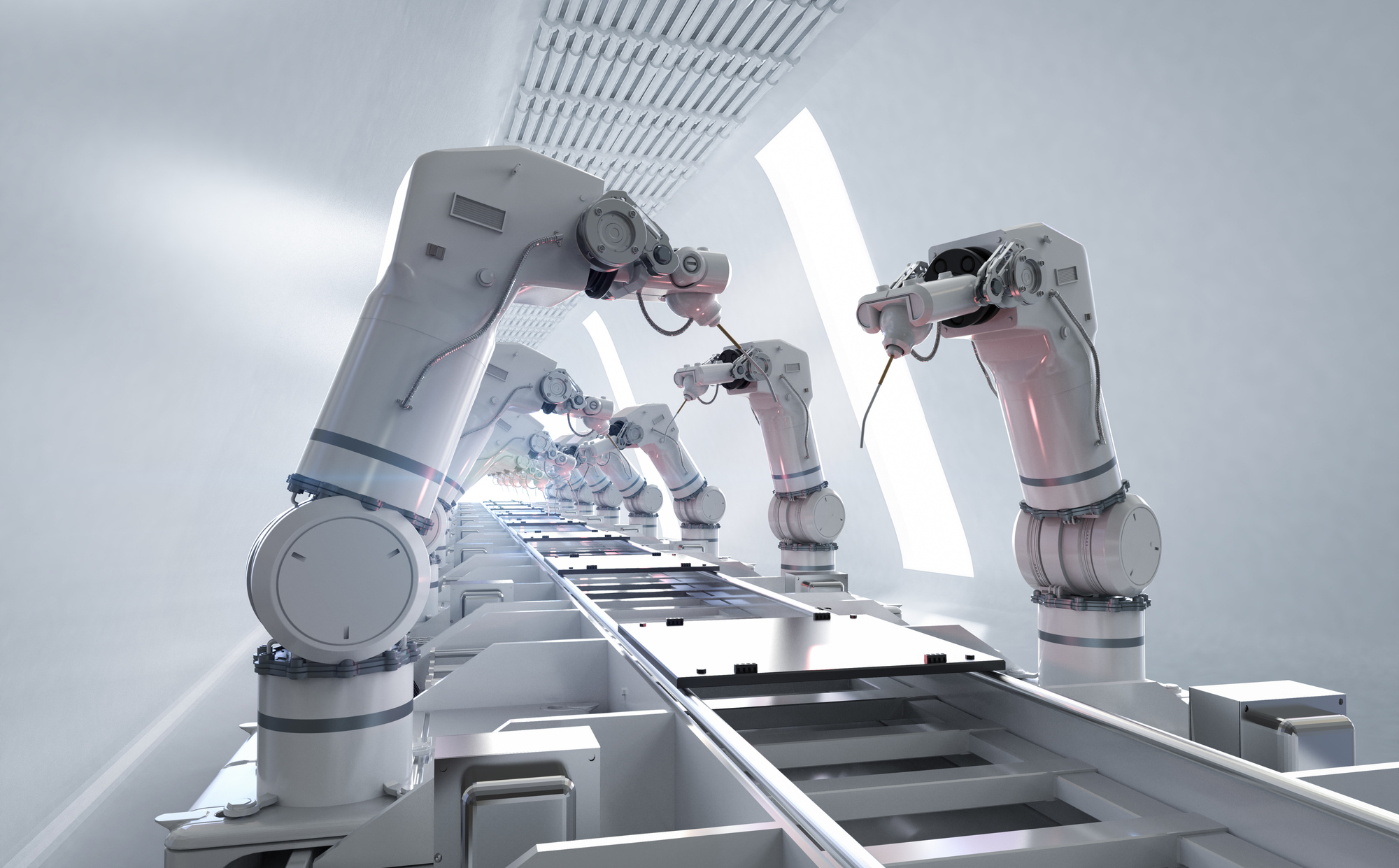
ジャストインタイム方式とは、「必要なものを必要なときに必要な分だけ」生産する効率的な生産方式です。
この記事では、ジャストインタイムのメリットとしての在庫管理の最適化、コスト削減、生産性の向上について解説します。
ほかにもジャストインタイムのデメリットや、企業の成功事例にも言及します。
記事の内容を参考にしながら、自社での活用のヒントを見つけてください。
ジャストインタイムとは
ジャストインタイム(Just-In-Time、JIT)とは、生産管理方式のひとつで、必要なものを必要なときに必要な分だけ生産・供給することを目指す方式です。
この方式により、業務の無駄を排除して効率的な生産を実現します。
ジャストインタイムの意味
「ジャストインタイム」の語源となる英語の「just in time」は、「ギリギリ間に合って」「ちょうどよいときに」などの意味を持つ言葉です。
例えば、英語で「I arrived just in time for the meeting」は、日本語で「私は会議にギリギリ間に合った」という意味になります。
このような意味合いが転じてビジネス用語となり、生産管理方式のひとつとして活用されるようになったのです。
ジャストインタイムの基本原則
生産方式のジャストインタイムは、以下の3つの基本原則があります。
- 後工程引き取り
- 工程の流れ化
- 必要数でタクトを決める
次項では、それぞれの基本原則について詳しく解説します。
後工程引き取り
「後工程引き取り」とは、必要なものを必要なときに必要な分だけ前工程から引き取り、前工程は引き取られた分だけ生産することを表します。
従来は生産計画通り順番に生産をおこない、完成したものから順に在庫となり、出荷という流れが一般的でした。
しかし、「後工程引き取り」では、先に顧客からのオーダーを受け、必要であることがわかった状態で必要な分だけ生産します。そうすることで、過剰在庫がなくなり、前工程でも無駄が発生しません。
工程の流れ化
「工程の流れ化」は、余分な在庫を持たないことを目的に平準化を行い、生産工程の中でできるだけ製品を停滞させずに流していくことを表します。
一個流しや小ロット生産を行うことで停滞を防ぐほか、ラインバランスの改善や同期化により工程間のバランスをとることで、効率的な流れの維持が可能となるのです。
必要数でタクトを決める
「必要数でタクトを決める」原則は、製品1個あたりの生産に必要な稼働時間を「タクトタイム」と定め、必要な人員数を決めることを表しています。
一般的な工場では、必要な製品数にかかわらず、毎日同じ人数が生産に関わることが多いです。そのため、無駄に作りすぎてしまう過剰生産、または在庫不足による欠品といった問題が生じることがあります。
このような問題を防止するためにも、生産量に応じた柔軟な生産ラインの構築は重要です。
ジャストインタイムの歴史
ジャストインタイムは、トヨタ自動車の創業者である豊田喜一郎が1938年(昭和13年)に完成した挙母(ころも)工場(現 トヨタ自動車本社工場)で導入したのが始まりです。
この方式は、当時の工場内の各工程で使われていたチェーンコンベアを同期化させることを目的としていました。
しかし、第二次世界大戦が勃発するなど情勢の悪化により、日本国内でも物資の不足が深刻化したため、ジャストインタイム方式による自動車生産は、一時的に困難を極める状況となったのです。
戦後になってようやく状況が改善されると、本来のジャストインタイムが進められるようになり、1954年にはトヨタ独自の「かんばん方式」が導入されました。
この方式は、後工程から必要な部品や資材を表示して供給する仕組みで、以降はトヨタ生産方式の中核としてジャストインタイムを支えるものとなったのです。
大量生産によるコスト削減が重視されていた、それまでの自動車生産の常識を覆すかのようなジャストインタイムは、当初世間には受け入れられませんでした。
しかし、無駄を無くして在庫を最小限に抑える革新的な生産方式として、その効率性と効果が認められるようになったことは想像に難くないでしょう。トヨタ自動車に限らず他の自動車メーカーやさまざまな産業分野で取り入れられることになったのは言うまでもありません。
現在では、ジャストインタイムは製造業界全体からその他の業界にまで幅広く普及しており、コスト削減と効率化を追求する多くの企業にとって重要な生産方式となっています。
ジャストインタイムのメリット
メリットの多いジャストインタイムは、多くの分野で導入されています。以下で主なメリットを詳しく解説します。
在庫管理の効率化
ジャストインタイム最大のメリットは、在庫管理の効率化です。従来の生産方式では、需要予測はあくまで予測でしかなく、機会損失を避けるために余分な在庫を大量にかかえる方法をとっていました。
特に自動車など1台あたりのコストが高い製品の場合、在庫を大量に持つことは大きなリスクを伴います。
また、在庫の数以外に、在庫を保管するスペースの問題もあり、倉庫の管理費用はばく大です。
食品など消費期限のある製品であれば、期限が切れた製品の廃棄処分を行う必要があります。
しかし、このようなあらゆる在庫の問題を解決するのがジャストインタイムなのです。
生産性向上
ジャストインタイムは、生産性向上のメリットもあります。無駄がなく効率的な生産ラインを構築することで、最適な人員数や工程数を確保することが可能となります。
また、毎日同じ数を生産するというよりは、需要に応じた生産が優先事項となるため、市場の変化などに対応する力を持ちます。
最適化された生産体制は、スタッフの負担を軽減し、高品質の製品を生産する原動力となるのです。
コスト削減
ジャストインタイムは、企業の大幅なコスト削減にも貢献します。在庫を最小限に抑えることにより保管費用を削減できるほか、無駄な生産をしないため、あらゆる生産コストを削減できます。
また、調達コストを削減できるのもメリットのひとつです。ジャストインタイムは必要なものを必要なときに生産すればよいため、資材の調達も必要な場合に限られます。
ジャストインタイムのデメリットと課題
ジャストインタイムは多くのメリットがありますが、デメリットや課題もあるのが現状です。
以下のような問題を解決できて初めて、ジャストインタイムは成功したと言えるでしょう。
サプライチェーンへの影響
ジャストインタイムは、サプライチェーンに大きな影響を及ぼします。必要なときに必要なだけ部品供給を行う必要があるため、部品を供給する企業への依存度が高くなりがちです。
逆に、部品製造会社は、提供先企業の生産に大きく左右されるため、柔軟な対応が求められます。その結果、立場が弱くなることもあるでしょう。
供給先と提供元が離れている場合、輸送コストの問題も無視できません。
必要なときに必要なだけ輸送しなければならないため、積載効率は二の次となります。信頼できる物流の確保も課題のひとつと言えるでしょう。
生産計画が難しい
ジャストインタイムは、生産計画が難しいのもデメリットです。
ある程度の予測は可能でも、突発的な要因が発生した場合には、需要予測も役立ちません。日頃から在庫を最小限に抑えているため、急な需要に応じられる生産計画の策定は困難です。
サプライヤーとの密な連携が成功のカギとも言えるジャストインタイムは、他社との連携なしに生産計画を立てることはできません。
品質管理が難しい
ジャストインタイムでは、品質管理が難しいとも言われています。
ジャストインタイムの三原則のひとつである「工程の流れ化」により、リアルタイムで生産が進行するため、不良品が発生しても対応が難しいのが実情です。
一度流れが決まってしまうと、品質向上のためのゆとりが少なく、改善を行うまで時間がかかります。同時にこのリアルタイムの生産の中で万全の品質管理をするには、コストがかかるため、効率化とのはざまで優先事項の選択を迫られることになるでしょう。
ジャストインタイム導入の6つのステップ
ジャストインタイムを自社に取り入れるためには、以下のステップを実施する必要があります。
ジャストインタイムの概念を理解する
ジャストインタイムを導入するためには、「必要なものを、必要なときに、必要な分だけ生産・提供する」という概念を理解する必要があります。従業員にも理解を促すため、教育や研修を行って定着させましょう。
現状分析
自社の現状を分析し、むだになっている箇所を特定します。生産工程やサプライチェーンなどを調査し、改善点を把握します。
目標設定
リードタイムの短縮やコスト削減、生産性の向上などを目指したジャストインタイムの導入目標を設定します。
プロセスの改善
生産工程の見直し、在庫管理の改善、サプライチェーンの最適化など、プロセスの改善を行います。
評価
ジャストインタイムを導入してうまくいったのか、またうまくいかない部分があれば何がいけなかったのか、評価します。評価をもとに改善点を特定しましょう。
改善
評価をもとに改善を行いますが、一度行ったら終わりではなく、現状分析から改善までを継続的に行うことが重要です。
ジャストインタイムの導入事例
トヨタ自動車で進められてきたジャストインタイムですが、トヨタ以外の企業でも導入された事例はないのか、小売業と飲食業で取り組んでいる企業を紹介します。
小売業
小売業でジャストインタイム方式を採用している代表的な企業はセブン-イレブン・ジャパンです。セブン-イレブン・ジャパンでは、「単品管理システム」として導入されています。
「単品管理システム」は、商品の発注数や陳列方法について立てた仮説を検証し、適時見直しながら最適化を図ります。商品供給の最適化により、無駄を最小限に抑えることが可能です。
同時に、売れ筋商品や売れ行きに応じた商品の補充システムである「プル販売システム」も採用しています。賞味期限が短いお弁当やパン、惣菜の廃棄を減らすため、1日数回の納品を行うシステムです。
これらシステムにより、セブン-イレブン・ジャパンでは顧客ニーズに応じて必要なときに必要な分だけ商品供給ができ、コスト削減につなげています。
飲食業
飲食業でジャストインタイム方式を採用しているびっくりドンキーは、食材の鮮度と品質を高めるため、必要なときに必要な分だけ食材を店舗に配送する仕組みを確立しています。
ハンバーグパティは、各店舗の翌日の需要予測に基づき、必要な量だけを全国の一次加工工場で製造しています。これにより、冷凍せずにチルド状態で毎日配送されるパティは、常に新鮮な状態で提供されるようになっているのです。
サラダに使われるカット野菜も、配送時刻から逆算して製造が行われています。
まとめ
ジャストインタイム方式とは、無駄を省く生産方式として多くのメリットがあります。
一方で、ジャストインタイム方式を導入するためには、サプライチェーンを巻き込んでの大がかりな計画が必要となることも否定できません。特に中小企業の場合は、企業全体への導入が困難な場合もあるでしょう。部分的・段階的に導入することが業務改善成功への近道となることもあります。
上記で解説したことを参考にしながら、ジャストインタイム導入についてどのような対策が必要なのか、ぜひ自社で話し合ってみてください。
関連記事
-
プロセス革新(プロセスイノベーション)とは?効果や事例をわかりやすく解説
プロセス革新(プロセスイノベーション)とは「業務プロセスや運用フローを見直し、効率化や成果向上を図るための新しい手法や仕組みを導入すること」です。この記事では、プロセス革新の基本的な考え方や具体例、導入のメリット、そして成功させるためのステップについて詳しく解説します。
-
技術革新とは?事例やイノベーションとの違いをわかりやすく解説
技術革新は、日々の生活やビジネスに大きな影響を与える変革です。この記事では技術革新の意味や歴史、もたらすメリットなどについて詳しく解説していきます。企業や社会で技術革新は、イノベーションと同じように扱われます。どのような違いがあるのか、具体例を交えながら掘り下げていくので、理解を深めて活用方法を考えていきましょう。
-
カーボンニュートラル時代を生き抜く中小企業の経営術とは?脱酸素との違いも
2050年のカーボンニュートラルの実現に向け、中小企業を取り巻く経営環境は大きく変化しています。取引先からの要請や規制強化など、さまざまな課題に直面する中、多くの経営者がどこから手をつければよいのか、費用はどうするのかといった悩みを持っています。この記事では、中小企業がカーボンニュートラルに取り組むための方法を学び、経営を守りつつ成長させるためのヒントをお伝えします。
-
リーン生産方式とは?トヨタ生産方式との違いなどをわかりやすく解説
リーン生産方式は、無駄を徹底的に排除し、高品質な製品やサービスを効率的に提供する手法として、世界の多くの企業が採用しています。この記事では、リーン生産方式の基本概念、導入ステップ、具体的な事例などを紹介します。
ビジネスにおけるリーン生産方式の重要性と活用法について理解を深めたいという方は、ぜひご一読ください。 -
SDGs経営とは?中小企業が取り組むべき理由と具体的アプローチ
SDGsは、もはや大企業だけの取り組みではありません。中小企業にとっても、SDGsの取り組みは、将来の事業継続に関わる重要な経営課題となっています。この記事では、SDGsの本質的な理解から、具体的な成功事例、中小企業ならではの実践方法などを紹介します。